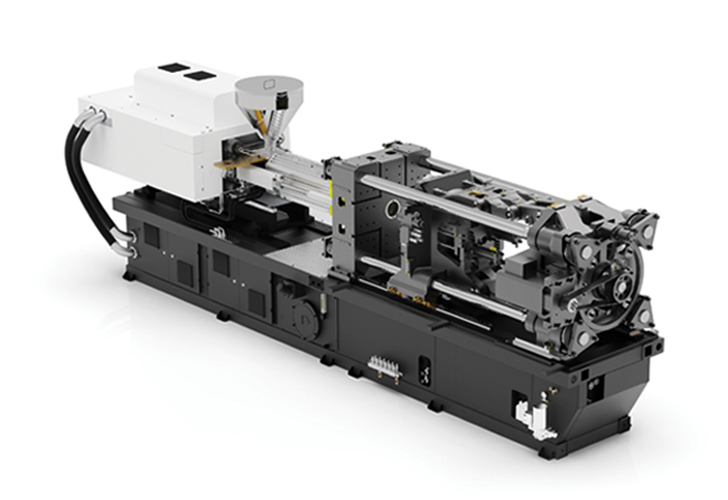
Enjeksiyon Prosesinde Yaşanan Problemler ve Çözümleri
Enjeksiyon makinesinin, kalıbın ve malzemenin performansı zaman, basınç ve sıcaklık değişkenlerine bağlıdır.
21-09-2022
Plastik enjeksiyon, sıcaklık yardımı ile eritilmiş plastik hammaddenin bir kalıp içine enjekte edilerek şekillendirilmesi ve soğutularak kalıptan çıkarılmasını içeren bir imalat yöntemidir.
Plastik Enjeksiyon Nedir?
Sıcaklık yardımı ile eritilmiş plastik hammaddenin bir kalıp içine enjekte edilerek şekillendirilmesi ve soğutularak kalıptan çıkarılmasını içeren bir imalat yöntemidir. Bu metot ile en küçük komponentlerden, bahçe mobilyalarına kadar çok çeşitli ebat ve kategorilerde plastik parçalar imal edilebilir.
Plastik Enjeksiyon Prosesinin Aşamaları
Basit olarak incelendiğinde bir plastik enjeksiyon parçasının imalat süreci şu aşamalardan oluşmaktadır.
KALIP KAPAMA
* Bir enjeksiyon makinesi aşağıdaki ana parçalardan oluşur:
* Kapama ünitesi (mengene)
* Enjeksiyon ünitesi ve kalıp kapama ünitesi
* Enjeksiyon ve soğutma
HAMMADDE ALMA (ERİTME)
Kovanın üstündeki ısıtıcılar kovanı, vidayı ve hammaddeyi ısıtır. Vida dönerken, hammadde hatvelerin arasında sıkışarak sürtünür ve ayrıca ısı yaratır. Dönen vidanın üzerinde yürüyen toz, granül, esnek şerit, yüksek viskositeli eriyik veya yarı sert hamur halindeki hammadde yavaş yavaş eriyerek vidanın ucundaki roket grubunun içinden geçerek, vidanın önünde birikmeye başlar. Hidromotor vidayı istediğimiz süratte çevirir, dönen vida konveyör gibi hammaddeyi yürütür ve önüne doldurur.
Öne dolan mal sıkışır ve vidayı geri itmeye başlar.
Geri basınç yatağı, merkezleme rulmanları ve büte rulman vidayı merkezler ve geri basıncını alır. Vida çok hızlı geri gitmesin ve eriyen malın içinde hava boşlukları kalmasın diye enjeksiyon silindirinden geri iletilen yağ, karşı tazyik valfi ile sıkıştırılır. Karşı tazyik miktarı hammaddenin cinsine göre değişir.
ENJEKSİYON
Vida dönerek geri giderken bilezik öne kayar ve rokete dayanır. Yüksük ve bileziğin arasından giren eriyik, bilezik ve roket arasından geçerek vidanın önünde depo edilir. Daha evvel programlanmış makine, kalıbı dolduracak kadar mal alındığını mikro switchler veya transduserler ile tespit ettiğinde mal alma, vidanın dönmesi ve geri gitmesi durur. Bu sefer enjeksiyon silindiri programlanmış bir sürat ve tazyik ile vidayı ileri iter.
Bilezik geri kaçarak yüksüğe basar ve bir çek valf gibi malın geri kaçmasını önler. Mal memeden ve yolluktan geçerek kalıbı doldurur.
Ütüleme: Parçanın istenen ölçülerde olması ve kalıpta soğuma esnasında çökmeyi ve çekmeyi önlemek için bellli bir tazyik belli bir süre vidaya bastırır. Bu aşamada kalıp içine enjekte edilmiş olan plastik eriyiğin, basınç uygulanarak kalıp boşluğunu iyice doldurması sağlanır. Plastik, kalıp içinde katı hale gelinceye kadar işlem devam eder. Kullanılan hammaddenin özelliğine, parça ebatlarına ve ağırlığına bağlı olarak işlemin süresi değişkenlik gösterir.
Soğutma: Zamanı dolunca tazyik kesilir. Kalıp soğutularak içerisindeki plastik ürünün donması sağlanır. Bu sefer donma zamanından istifade edilerek yeniden vida dönmeye başlar ve geri giderken bir dahaki sefere basılacak mal alınmaya başlar. Mal alma bitince programlı bir şekilde enjeksiyon silindirinin ön yüzüne tazyikli yağ verilir, vida 5 mm – 10 mm geri çekilerek meme ağzındaki mal geri emilir. Yolluk içindeki mal meme ağzındaki maldan koparılır.
Kalıp açma: Kalıp açıldığında, kalıplanmış madde dişi kalıptan kurtulur ve yolluk kopması olmaz. Yolluk boşaldığında, meme içindeki mal kendiliğinden akıp yolluğu tıkamaz veya kalıp içine akmaz. Bu işlem cereyan ederken meme ve kovanın üstü kontrollü bir şekilde ısıtılır.
Çıkarma: İticiler vasıtası ile bitmiş parça kalıptan çıkarılır. Enjeksiyon makinelerinin birçok bileşeni (tekli yada çoklu) yatay ya da dikey yapılandırılmış olarak birçok farklı konfigürasyonları vardır. Ancak ne olursa olsun tüm enjeksiyon makinelerinde genel süreç hep aynıdır. Yukarıda anlatılan süreç tüm enjeksiyon makineleri için geçerli proses sürecidir.
ENJEKSİYONDA STROK DURUMUNA BAĞLI ISI AYARLANMASI
Her plastik hammaddenin, erimeye hazırlık, erime ve kalıplama derecesi vardır. Bu sebepten kovanın üzerinde en az 3 adet ısı bölgesi bulunur ve termokuplar ile bu dereceler kontrol edilir. Vida dönerek mal alır eritir ve enjeksiyondan önce önüne stok eder. Bu hareket ısıtmaya direkt etki eder. Vida geri giderken boyu kısalmakta ve eritme kabiliyeti azalmaktadır. Bu durumda da kovan üzerindeki ısı dağılımları optimum şekilde ayarlanmaktadır.
Aşağıdaki şekilde strok kullanım durumuna bağlı, kovan ısıtma bölgeleri için sıcaklık değerlerinin ayarlanma grafiği gösterilmektedir. Eriyik malzeme memeden kalıplanacak derecede çıkmaktadır. Vidanın geriye hareketi ve limiti enjeksiyon makinesinin mal basma kapasitesini verir. Bu hareket normalde vida çapının 4 mislinden fazla yaptırılmaz. Kaliteli baskılara ulaşmada strok için vida çapının 3 katından çok, 1 katından az hareket yapılmamalıdır ve kapasite bu limitler içinde tutulmalıdır.
ENJEKSİYON MAKİNESİ VE BÖLÜMLERİ
* Hidrolik Motor
* Besleme Hunisi
* Sabit ve Hareketli Plakalar
* Mengene ve Hidrolik Piston (Kalıp Kapama Silindiri)
* Kovan ve Vida
* Kolon Mili
* Kalıp Ünitesi
Enjeksiyon Ünitesi
Enjeksiyon ünitesinin, yani enjeksiyon grubunun ana amacını plastik malzemeyi eritmek ve kalıba basmak şeklinde özetleyebiliriz. Sürekli aynı ağırlıkta ve aynı kalitede parça üretimi için kalıba basılan malzeme miktarı her seferinde aynı olmalıdır. Bunun için enjeksiyon grubu sürekli aynı sıcaklıkta homojen malzeme baskısı yapabilmelidir.
Enjeksiyon Ünitesi şu elemanlardan oluşur;
* Hidrolik Motor
* Besleme Hunisi
* Kovan ve Vida Grubu
Mengene Ünitesi
Bir enjeksiyon makinesinin mengene ünitesinin başlıca görevleri;
* Kalıbı kapamak,
* Enjekte edilen malzemenin ürün haline dönüşmesi için kalıbı kapalı tutmak,
* Ürünün çıkarılması için kalıbı açmaktır.
* Bir enjeksiyon makinesinin mengene sistemi yatay prese benzer.
Bu sistemin ana kısımları; Bir sabit plaka, bir hareketli plaka, bir L-plaka (destek plakası) ve hareketli plakanın hareketini sağlayan bir tahrik sisteminden meydana gelir. Bu tahrik sistemi de genelde hidrolik bir sistemdir.
KALIP
Enjeksiyon işleminin belki de en önemli elemanı kalıptır. Çünkü baskı kalıba yapılır. İki veya daha fazla parçadan oluşan kalıplar, üretilen her parça için farklı yapıda ve özelliktedir.
Bir kalıp;
* Erimiş malzemenin kalıp boşlukları içinde rahatça akışını sağlayabilmeli,
* Erimiş malzemeye istenen son şeklini verebilmeli,
* Son şeklini almış malzemeyi soğutup ürün haline getirebilmeli,
* Çapraz örgülü malzemeleri lastik gibi ısıtabilmeli,
* Ürünü sağlıklı bir şekilde dışarı alabilmelidir.
Bir kalıp genelde dört ana parçadan oluşur:
1.Yolluk sistemi: Eriyik malzemeyi alır ve boşluklara dağıtır.
2. Kalıp boşluğu: Eriyik malzemeye son şeklini verir.
3. Isı sistemi: Eriyik malzemeyi ısıtır ve soğutur.
4. İtici sistemi: Ürün haline gelmiş malzemeyi kalıp dışına atar.
Plastiğin Erime Karakteri, Erime davranışı ve Kovan-Vida Sistemlerinin Eriyik Kalitesine Etkisi
Polimerler ısı ve shear stres etkisi altında, kristal yapılarını ve bağ yapılarını değiştirerek fiziksel olarak dönüşüm gösterirler. Fiziksel hal değişimini ve bu değişim karakterini etkileyen en önemli şey elbette kimyasal ve molekül hareketleridir. Aynı kimyasal bileşime sahip polimerlerde dahi yarı kristalin ya da amorf yapıda olunması bu karakteri mutlaka değiştirir.
Polimerik malzemeleri karakterize etmek için kullanılan iki ana geçiş sıcaklığı vardır:
Erime Sıcaklığı (Te) Ve Camsı Geçiş Sıcaklığı (Tg)
Kristalleşebilen polimerlerin % 100 kristal yapıda olmasının ancak teorik olarak mümkün olabileceğini belirtmiştik. Yarı kristal bir polimerin kristalize olmuş zincirlerinin erimeye başladığı sıcaklık, polimerin erime sıcaklığı olarak kabul edilir. Amorf yapıda bulunan kısımların ise soğuma sırasında yumuşak kauçuğumsu yapıdan, sert, kırılgan ve katı (rijit) camsı yapıya geçtiği sıcaklığa ise camsı geçiş sıcaklığı denir.
Polimerin ısı karşısındaki davranışları, yapılarında amorf ya da kristal bölgelerin varlığına yakından bağlıdır. Amorf polimerler ısıtıldıklarında önce camsı geçiş sıcaklığından geçerek camsı yapılardan kurtulur ve elastiki hale kavuşurlar. Daha yüksek sıcaklıklara ısıtıldıklarında ise zamksı davranışa ve sıvılaşmaya uğrarlar. Bu hareketlerinin artışından kaynaklanan bir akışkanlık, ya da sıvılaşmadır.
Yarı-kristal polimerler ise önce camsı geçiş sıcaklığından geçerek camsı yapıdan elastiki yapıya ulaşırlar. Daha yüksek sıcaklıklarda ise amorf yapılarının içinde oluşan kristal yapıları erimeye başlar ve eriyik halde bir polimer oluştururlar.
Erime esnasında polimere uygulanacak yüksek ısı, yüksek shear stres ya da basınçtan dolayı ya da bunun tam tersi durumdan ötürü polimer eriyiğinin kalitesi etkilenecektir. Polimerin erime prosesinin gerçekleştiği kovan-vida grubunda doğru dizayn ve doğru malzeme kullanımı son derece önemlidir.
Plastik ürün üretiminde plastiğin erime mekanizması ve karakterine uygun olmayan bir yöntem ile kaliteli bir eriyik yapısı elde edilemez. Plastiğin eriyik karakterine uygun bir kovan-vida grubu seçilmelidir. Her plastik hammadde ve her prosese özel kovan ve vida dizaynları olduğu gibi birçok polimeri işleyebilecek üniversal dizaynlarda mevcuttur.
Enjeksiyon Uygulamalarında Kovan-Vida Sistemlerinin Önemi
Plastik makinelerinde plastiğin eritildiği ve şekil verilebilir hale getirildiği kısım kovan ve vidadır. Dolayısı ile plastiğin eriyik kalitesine, homojenliğine ve bu eriyikten elde edilecek ürünün kalitesine doğrudan en fazla etki eden bileşen her zaman kovan ve vidadır. Plastik ürünün kalitesinde eriyik kaynaklı yaşanan problemlerin %80 inde problemin kaynağı, kovan ve vida gruplarının yanlış dizayn ya da aşınma sonucu görevi yerine getirmemesindendir. Bu durum kova ve vida sisteminin plastiği ergitme, taşıma ve sıkıştırma işlerini üstlenmiş olması dolayısı ile en fazla yorulmaya ve aşınmaya maruz kalmasının bir sonucudur.
Polimerlerin erime proseslerinin gerçekleştiği kovan ve vida grubunda doğru dizayn ve doğru malzeme seçimi son derece önemlidir. Farklı prosesler, farklı plastik malzemeler ve farklı kapasite ihtiyaçlarına bağlı olarak, eriyik kalite unsurunu en üst seviyede tutabilecek şekilde tasarlanan kovan ve vida sistemlerinin, bir çok polimeri işleyebilecek şekilde üniversal dizaynları da bulunmaktadır.
İlgili proses ve polimer karakterine uygun olmayan kovan ve vida kullanımından dolayı şu sorunların yaşanması muhtemeldir.
* Yeterli erime sağlanamaz.
* Uygun eriyik kalitesine ulaşılamaz.
* Eriyikte homojenlik sağlanamaz.
* Üründe yeterli mekanik dayanım elde edilemez.
* Düşük kapasite ve düşük enerji verimliliği ile üretim yapılır.
* Kovan ve vida sistemlerinde hızlı aşınma ve yıpranmaya sebep olur.
* Kalıp ve ona bağlı tüm bileşenlerde bir çok hasara sebep olabilir.
Günümüzde gelişen teknolojinin de getirdiği avantajlar ile plastik işleme proseslerinin ihtiyaçlarını karşılayacak bir çok AR-GE çalışmalara yapılmaktadır. Konusunda uzmanlaşmış ve üstün tasarım kabiliyetine sahip kurumlar ve kişiler tarafından yapılan bu AR-GE çalışmaları sonucunda kovan-vida sistemlerinde yüksek ergitme kabiliyeti, yüksek kapasite ve performans, üstün aşınma direnci ve düşük üretim maliyeti avantajı sağlanmış, basit yapılı ürünlerden en kompleks ve karmaşık karakterdeki ürünlere kadar olan tüm ihtiyaçlara cevap verilebilir duruma gelinmiştir.
Enjeksiyon Uygulamalarında Kovan-Vida sistemlerinin Şekil Tanımı ve Temel Boyutlandırma
Enjeksiyon uygulamalarında kullanılan kovan-vida sistemlerinde, görüntü itibari ile hangi bölümlerden oluştuğu ve temel boyutlandırmada kullanılan terim ve tekniklerin bilinmesi, hem üretici hem de kullanıcıların ortak bir dilde buluşmasını sağlamakta ve faydalı olmaktadır.
Dünyada Plastik teknolojileri adı altında yapılar tüm çalışmaların, ortak dilde konuşulması ve belirli standartlarda uygulanabilmesi için EUROMAP normları oluşturulmuştur. Bu standartlar dahilinde enjeksiyon kovan-vida sistemleri de plastik işleme yeteneğini sınıflandırma ve boyutlandırma açısından çap (D) ve boy (L) ölçülerinin belirli bir oranına bağlı olarak mal edilmektedir.
L/D olarak tanımlanan bu oran, vide efektif boyunun çapına oranı olup vidanın ilgili plastiği eritme ve işleme boyunu göstermektedir.
Basit yapılı bir enjeksiyon kovanı ve vidası ele alındığında, vidanın sürücü boyu haricinde kalan diğer kısmı hatve boyu L (genel) olarak adlandırılır. Ancak L/D oranındaki L boyu, kovanın penceresinden itibaren başlayan yani plastik hammaddenin erimeye başladığı L (efektif) boyudur. Her proses için standart oluşturulmuş olan bu oranla gelişen plastik teknolojisi ile farklılıklar da gösterilmektedir.
Enjeksiyon Uygulamalarında Kovan-Vida Sistemleri ve Çalışma Prensibi
Enjeksiyonda kullanılan kovanlar, proses sırasında oluşan yüksek basınca karşı dayanıklılık ve kararlılık göstermelidir.
Enjeksiyon sırasında, yüksek enjeksiyon basıncına bağlı olarak kovan içi çapı esneyerek genişleme eğilimi gösterir.
Kovan dizaynı, malzeme seçimi ve sertleştirme metodu kovan iç çapı ile roket grubu bileziği arasındaki dar boşluğu koruyacak şekilde seçilmeli, hassasiyet sürekliliğini sağlama açısından aşınma direnci yüksek malzemeler kullanılmalıdır.
İdeal enjeksiyon prosesi için, kovan iç çapı ile vida dış çapı, kovan iç çapı ile roket grubu bilezik dış kapı arasında hassasiyetle seçilmiş dar boşluklar bırakılmalıdır.