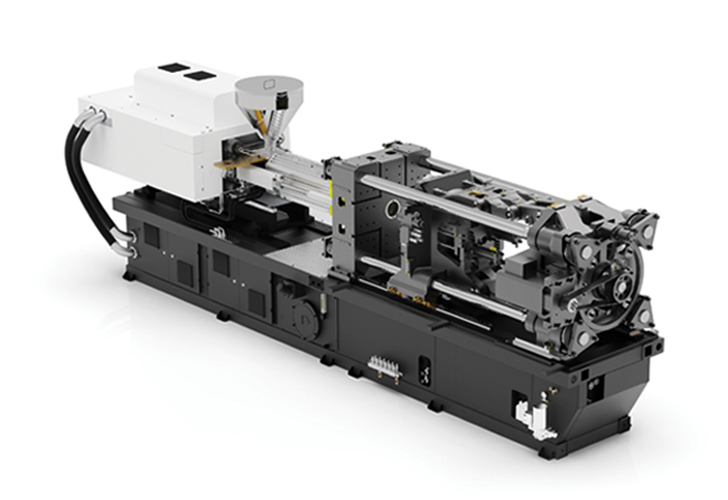
Enjeksiyon Prosesinde Yaşanan Problemler ve Çözümleri
Enjeksiyon makinesinin, kalıbın ve malzemenin performansı zaman, basınç ve sıcaklık değişkenlerine bağlıdır.
21-09-2022
Plastikler moleküler yapılarına bağlı farklı nem çekme kapasitelerine sahiptirler.
Plastik Hammaddelerde Neme Duyarlılık Ve Az Duyarlılık Nedir?
Plastikler moleküler yapılarına bağlı farklı nem çekme kapasitelerine sahiptirler. Bu özellikleri nedeni ile neme duyarlı ve neme az duyarlı diye iki gruba ayrılır.
NEME AZ DUYARLI HAMMADDELER
PE,PP,PS,PVC,PPS vb. nemi çekirdeğine kadar almaya yatkınlığı olmayan, sadece dış çeperinde oluşan nemi sıcak hava ile ısıtıldığında atabilen hammaddelerdir. Bu tip hammaddelerin kurutulması için sıcak havalı kurutucular tercih edilir.
NEME DUYARLI HAMMADDELER
PA,PC,PET,PBT,ABS,PET-G,PMMA,POM vb. ortam havasına maruz kaldığında moleküller yapısı gereği nem almaya yatkınlığı olan ve sadece sıcak hava ile ısıtılarak nemini atamayan hammaddelerdir. Neme duyarlı hammaddeler çevrelerinde bulunan su buharını çekirdeklerine kadar çekmeye eğilimlidir. Bu tip hammaddelerin kurutulması için nem alıcılı kurutucular veya vakumlu kurutucular tercih edilebilir.
Plastik Hammaddeler Neden Kurutulmalıdır?
Plastiklerin en önemli problemlerinden biri nemlenmedir. Plastik hammaddelerin istenilen yapısal ve görsel özelliklerine ulaşabilmesi için ürün haline gelmeden önce bünyesindeki nemi atması için bazı kurutma işlemlerinden geçmesi gerekmektedir. Plastik hammaddeler işlenmeden önce cinsine göre uygun bir kurutucu ile yeteri kadar kurutulmadığında nemin ürün üzerindeki olumsuz etkileri aşağıdaki şemada görülmektedir.
DÖKME YOĞUNLUĞU NEDİR?
Dökme yoğunluğu, belirli bir hacme sığan hammaddenin ağırlığıdır. Fiziksel olarak, 1 litre kabın içine konulan hammaddenin kilogram olarak ağırlığıdır. Bu sebeple aynı çeşit olsa dahi granül, kırma, toz şeklindeki malzemeler farklı dökme yoğunluğunda olabilir. Örneğin, granül şeklindeki PET hammaddesinin dökme yoğunluğu 0,85 kg/litre iken kırılmış PET şişe dökme yoğunluğu 0,2 ile 0,35 kg/litre arasında değişebilir.
Öte yandan, katı haldeki hammaddenin yoğunluğu ile eriyik haldeki yoğunluğu farklıdır. Eriyik hammaddenin yoğunluğu her zaman katı haldeki granül, kırma veya toz formundaki dökme yoğunluğundan fazladır; çünkü granül, kırma ve toz halde iken hammaddenin arasında hava kalır ve bu da belirli hacimde daha az ağırlıkta hammadde bulunmasına sebep olur. Örneğin, PET granülün dökme yoğunluğu 0,85 kg/litre iken eriyik PET malzemenin yoğunluğu 1,1-1,2 kg/litre aralığında değişebilir.
ÖNEMLİ NOT: Plastik hammadde kurutma silolarının seçimi yapılırken hammaddenin eriyik yoğunluğu değil, dökme yoğunluğu kullanılarak hesap yapılmalıdır.
Farklı hammaddelerin dökme yoğunlukları ‘’4.Hammaddeler’’ bölümünden incelenebilir.
KURUTMA PARAMETRELERİ NELERDİR?
Hammaddenin nemi atması dış rutubet şartlarına bağlıdır. Kuru ve sıcak havanın bulunduğu düşük basınçlı ortama giren hammadde iç rutubet basıncı daha fazla olduğu için nemini dışarıya vermeye başlar. Bu işlem iç ve dış basınçların eşitlenmesine kadar devam ettiğinden hammadde dış ortam kuruluk oranına ulaşana kadar nemini atma eğilimindedir ve buna ulaşıldığı anda hammadde kurumuş olur.
Seçilecek olan kurutucu tipine bağlı olarak kurutma parametreleri değişkenlik göstermektedir.
SICAK/KURU HAVALI KURUTUCULAR İÇİN KURUTMA PARAMETRELERİ
SICAKLIK: Hava ile kurutma tekniğinde ortam havasının veya kurutulmuş havanın hammadde cinsine göre belirli sıcaklığa çıkarılması ve hammaddenin bu sıcaklığa maruz kalması gerekmektedir. Zira, her hammaddenin polimer zincir yapısı su moleküllerini serbest bırakacak farklı sıcaklık değerlerine sahiptir. Hammadde cinsine göre bu sıcaklık 60°C ile 180°C arasında değişebilir.
ZAMAN: Hammaddenin belirtilen sıcaklığa maruz kalması gereken süredir. Bu süre hammaddenin moleküler yapısına ve ne kadar nemli olduğuna göre 1 saat İle 6 saat arasında değişir. Kurutma süresinin fazla olması ise hammaddenin kimyasal veya görsel olarak bozulmasına sebep olduğundan fazla kurutmadan kaçınılmalıdır.
KURU HAVA: Neme duyarlı plastik hammaddeler için kuru hava ile kurutma zorunludur. Bu parametre çoklukla çiylenme noktası ‘’dew point’’ terimi kullanılarak betimlenir. Çiylenme noktası sıcaklığı ne kadar düşük olursa hava içindeki nem miktarı o kadar azalacak ve hammaddenin çekirdeğinde sıkışan nem o kadar dış çepere doğru hareket etmeye zorlanacaktır. Böylece hammadde nemden daha iyi arındırılıp daha iyi kurutulmuş olacaktır. Neme az duyarlı hammaddeler için sadece sıcak hava ile kurutma yeterlidir, kuru hava gerekli değildir.
HAVA DEBİSİ: Sıcak havanın kurutma silosu içindeki sirkülasyon hızı da diğer bir para metredir. Bu debi az olursa sıcak havanın silo içinde dağılımı homojen olmaz ve dolayısı ile her hammadde eşit kurutulmaz. Öte yandan, havanın nemli hammaddeye nüfuz etmesi ve kurutma süresi uzar.
HAMMADDE ŞEKLİ VE DÖKME YOĞUNLUĞU: Kurutulacak hammaddenin şekli ve dökme yoğunluğu kurutma cihazı seçilirken dikkat edilmesi gereken parametrelerdir. Zira, hammaddenin yukarıda belirtilen sıcaklıkta ve sürede, kuru hava veya sıcak hava ile kurutulması işlemi bir kurutma silosu içinde yapılır. İstenilen verimde kurutma için bu silonun hacminin yeteri kadar büyük olması gerekir. Silo hacminin hesabında hammaddenin şekli (granül, deşe, kırma, vb.) ve dökme yoğunluğu önemlidir.
Vakumlu Kurutucular İçin Kurutma Parametreleri
Sıcaklık: Vakum tipi kurutucularda sıcaklık vakum işlemi öncesi hammaddenin ısıtılması için kullanılır. Hammaddenin kurutulması için asli faktör değildir.
Vakum: Vakum tipi kurutucuların öncelikli kurutma parametresidir. Hammaddenin içindeki nemin vakum altında emilmesi prensibine göre çalışan bu tip kurutucularda hammadde ön ısıtmadan sonra vakum altına alınır.
Zaman: Vakum süresi hammadde cinsine göre 15 dakika ile 45 dakika arasında değişir. Bu süre aynı zamanda kurutma süresi anlamına gelir. Vakum altında fazla kurutma söz konusu olmadığından kuru havalı kurutucularda yaşanan kimyasal veya görsel bozulmalar yaşanmaz.
Kurutulacak Malzemenin Şekil Ve Yapısının Kurutucu Seçimine Etkisi Nedir?
Kırma Formlu Hammaddelerin Etkisi: Plastik hammadde granül formunda olduğu gibi kırma formunda da kullanılır. Kırma makineleri ile kırılan ürünler ve diğer üretim fireleri kırma makinelerin elek ölçüsüne bağlı olarak farklı boyutlarda olabilir. Kırılan ürün veya fire eğer ince ise kırma sonucu pul şeklinde oluşur ve deşe (İngilizce karşılığı flake) olarak adlandırılır.
Kurutulacak hammaddenin eriyik yoğunlukları aynı olsa dahi granül, normal kırma ve pul şeklinde kırmanın kurutma silosunda aynı hacimdeki ağırlıkları farklıdır. Kırma hammadde bir kez eritilip tekrar katılaştığı için işleme prosesine bağlı olarak moleküler yapısı az da olsa değişir. Bu sebeple, kurutma parametreleri de bu oranda değişir. Öte yandan, granül hammadde kurutmadan önce nemden arındırılmış orijinal ambalajından çıkarken, kırma makinesinden çıkan malzeme genelde ortam şartlarında neme doyar ve bu sebeple kurutulması için daha fazla zaman ve kuru havaya ihtiyacı vardır.
Hammadde Katkılarının Etkisi: Plastiğin birçok diğer hammaddenin yerini aldığı günümüzde katkı olarak adlandırılan ve renklendirme, kaydırıcılık, sertlik, dayanıklılık gibi farklı fiziksel ve kimyasal özelliklerin oluşturulmasını sağlayan birçok katkı çeşidi daha vardır. Bu tip katkıların dökme yoğunlukları da farklıdır. Kalsit katkılı hammaddelerin bünyelerinde yüksek oranda neme çok duyarlı kalsit bulunmasından kaynaklı kurutma parametreleri değişebilmektedir. Örneğin PE hammaddesinin işlenebilmesi için sıcak havalı bir kurutucu ile 1 saat kurutulması yeterli olurken; kalsit katkılı bir PE hammaddesinin 3-4 saat desikant kurutucular ile kurutulması gerekir.
Polyamid hammaddenin dökme yoğunluğu 0,65 kg/lt iken; cam elyaf oranına bağlı olarak dökme yoğunlukları 0,75 kg/lt olabilmektedir. Dolayısıyla aynı kurutma kapasitesi için cam elyaf katkılı polyamidin kurutma silosu, cam elyafsız polyamidin kurutma silosundan daha küçük seçilebilir.
Kurutucu Montaj Şekilleri Nelerdir? Bu konu ile ilgili karar verilirken unutulmaması gereken en önemli unsur kurutucudan çıkan kuru hammaddenin plastik işleme makinesinin vidasına ulaşmadan tekrar nem almasının engellenmesidir. Bu sebeple kurutucunun işleme makinesine en yakın yere konumlandırılması gerekmektedir. Diğer seçim kriterleri ise kurutucunun cinsi, yüksekliği, boyutları ve ağırlığıdır.
MAKİNE ÜSTÜ MONTAJ
Sıcak havalı kurutucuların en çok tercih ettiği montaj şekli plastik işleme makinesinin vidasına hammaddenin boşaldığı boğaz bölümüdür. Kuruyan hammaddenin nem almadan ve halen sıcak iken direkt olarak işlenmesini sağladığından ve işletme içinde yer kaplamadığından çok tercih edilen bir montaj şeklidir.
DİKKAT EDİLMESİ GEREKEN HUSUSLAR;
* Kurutucunun ve varsa üzerindeki emicinin yüksekliğinin vinç yüksekliğinin altında kalması
* İçindeki hammadde dahil kurutucu ağırlığının özellikle enjeksiyon makine kullanımında hareketli vida grubunun hareketini zorlamaması.
* Zaruri vida bakım ve değişimlerinde kolay demonte edilebilmesi
* Kurutucunun kendi bakımının ve hammadde değişimlerinde temizliğinin yapılması için iş güvenliği kuralları çerçevesinde platform ve merdiven kullanılmasıdır.
PLATFORM ÜSTÜ MONTAJ
Eğer kurutma silosu büyük ise içindeki hammadde ile birlikte ciddi bir ağırlığa sahip olacağından vidanın boğazına direkt bağlanması engel ve tehlike oluşturabilir. Hammadde değişimi ve silonun boşaltılması işlemleri de bir hayli zorlaşır. Bu nedenle işleme makinesinin vida boğazının üstüne taşıyıcı bir platform yapılarak kurutucunun yükü platforma verilir.
Bu yöntem de diğer makine üstü montaj şeklidir. Bu durumda kurutucu çıkışı ile vida arasında esnek bağlantı hortumları kullanılabilir.
Kurutucu ile vida arasındaki boşluğun diğer bir avantajı da boya (katkı) dozajlama cihazı kullanımı gerektiğinde bu aralıktan faydalanabilmesidir. Ancak bu yöntemde yükseklik konusuna dikkat edilmelidir. Gerek yüksek kapasiteli sıcak havalı ve gerekse nem alıcılı (desikant) kurutucuların yükseklik sıkıntısı olmayan tesislerde en verimli konumlandırma yöntemlerinden biri budur.
MAKİNE YANI MONTAJ
Yukarıda belirtilen vida üstü montaj şekilleri uygulanamıyorsa diğer bir yöntem de kurutucu cihazının işleme makinesinin yanına konumlandırılıp kurutulan malzemenin bir emici vasıtası ile işleme makinesinin vidasına beslenmesidir.
Çokça tercih edilen bu yöntemin iki ana dezavantajı vardır.
MERKEZİ SİSTEM MONTAJ
Üretimde kullanılan hammadde ve işleme makinesinin fazla olduğu tesislerde kurutucunun makine üzerinde veya yanında bulunmasının bazı zorlukları vardır. Bunlar; hammadde değişiminin çok yapılması, tesis içinde alan yetersizliği (zemin alanı veya yükseklik), tesisin içine hammaddenin taşınmasının getirdiği zorluklar ve kirlenme vb. bu gibi durumlarda hammaddenin merkezi bir odada kurutulması gerekir. Bu odada kurutulan hammadde buradan arabalarla alınarak işleneceği plastik makinesine götürülürken nem alacağı için merkezi hammadde kurutucu sistemi ile plastik işleme makineleri arasında merkezi besleme sistemi kurulması gerekir. Bu sistemde en çok dikkat edilmesi gereken konu hammaddenin taşınması esnasında nem almasının engellenmesi ve hammadde değişimlerinde boru hattının çok iyi temizlenmesidir.