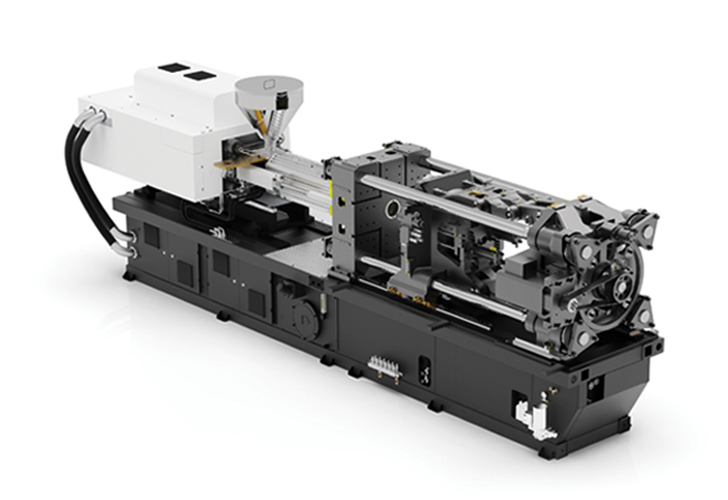
Enjeksiyon Prosesinde Yaşanan Problemler ve Çözümleri
Enjeksiyon makinesinin, kalıbın ve malzemenin performansı zaman, basınç ve sıcaklık değişkenlerine bağlıdır.
21-09-2022
Aşınma katı yüzeylerden malzeme azalması, malzeme kaybı ya da bu yüzeylerin kullanılmaz hale gelmesidir.
Aşınma Türleri
Aşınma, genel olarak amrazyon, erozyon, adhezyon ve yüzey yorulması olarak sınıflandırılmaktadır. Bu sınıflandırma, aşınan yüzeye gelen yük, aşındırıcı parçacığın boyutu ve türü, temas şekli ve temas geometrisi gibi etkenler dikkate alınarak yapılmıştır. En fazla aşınma kaybı genellikle abrazyon aşınması türlerinde görülür. Aşınma katı yüzeylerden malzeme azalması, malzeme kaybı ya da bu yüzeylerin kullanılmaz hale gelmesidir. İki yüzey yük altında kayma ve yuvarlanmaya maruz kaldığında sürtünme ve aşınma olaylarının meydana gelmesi kaçınılmazdır. Makine elemanlarında en sık karşılaşılan aşınma türleri abrazyon, erozyon, adhezyon ve yüzey yorulması aşınmalarıdır.
Abrazyon Katı bir yüzeye karşı veya yüzey boyunca hareket eden sert parçacıkların yapmış olduğu aşınmadır. Karşılaşılan aşınma türlerinin %60’ı abrazyon aşınmasıdır. Abrazyona neden olan parçacık ya da parçacıklar aşınmaya maruz kalan yüzeyden daha serttir. Aşındırıcı parçacıkların yüzeyde yapmış olduğu hasar tipleri: kayma, yuvarlanma, tıraşlama, kesme, çizme, öğütme zımparalamadır.
Adhezyon İki katı yüzeyin aralarında yerel bir temas bağı oluşturarak yapışması söz konusudur. Yapışan yüzeylerin yük, hareket ve titreşim gibi sebeplerle birbirinden ayrılmakta ve beraberinde yüzeyden kütlesel olarak parçalar kopmaktadır.
Kovan Vida Sistemlerinde Aşınma Mekanizması
Kovan Vida sistemlerinde kovan ile vida arasındaki temas ve sürtünmeden dolayı adhezyon meydana gelirken kovan ve vida içerisindeki hammaddenin yüzeylerle temasından dolayı ise abrazyonla aşınma meydana gelir. Ayrıca bu fiziksel aşınmaların yanı sıra kimyasal olarak korozif etkiler sebebi ile korozyon meydana gelir. Aşınmaları engellemek için kovan-vida sistemlerinde aşınma mekanizmalarını kendi içerisinde gözden geçirmeliyiz.
Adhezif Aşınma
Yüzeyler ne kadar iyi işlenmiş ve parlatılmış olursa olsun, mikroskop altında incelendiğinde küçük çukurlar ve tepeciklerden meydana gelmiş bir yapı görünür. Birbirine temas eden iki yüzey arasında sürtünme ile oluşan ısı ,aslında iki yüzey arasında bir mikrokaynak oluşmasına sebep olur. Bu mikro kaynak sebebiyle yüzeylerde oluşan kopmalar ve çukurlaşmalar iki yüzeyin birbirine teması devam ettiği sürece meydana gelir.
Sonuç olarak ; adhesif aşınma, her iki metalin birbirinin yüzeylerinde mikro kaynaklar yaratabilme kabiliyetlerinin yüksekliğine ve bu materyallerin kendi yarattıkları abrasif mikro kaynak parçacıklarının yüzeylere verildikleri zarara dayanma kabiliyetine bağlıdır.
Abradif Aşınma
Genel olarak malzeme yüzeylerinin kendisinden daha sert olan partiküllerle basınç altında etkileşip sert partikülün malzeme yüzeyinden parça koparmasına abrasif aşınma denir.
Kovan ve vida arasında iki tür mekanizma ile abrasif aşınma meydana gelebilir;
* Kovan ile vida yüzeyleri arasında pürüzlülükten doğan ve sert olan yüzeyin daha yumuşak olan yüzeyi aşındırması ile sonuçlanan bir aşınma gözlenir. Bu sebeple kovan ve vida malzemelerinin benzer sertliğe sahip olmasına dikkat edilmelidir.
* Plastik içerisindeki sert dolgu malzemeleri veya cam elyaf gibi katkılar kovan iç yüzeyi ile vida üzerinde taşınırken bu sert partiküller kovan ve vida ile temas ettikleri yüzeyleri parçacıklar kopararak aşındırırlar.
Korozif Aşınma
Korozif aşınma malzeme yüzeyinde meydana gelen kimyasal reaksiyonlar sonucu malzeme yüzeyinden parçacıkların kopması ile açıklanabilir. Korozif malzeme çalışılan sistemlerin özellikle çalışılan malzemenin korozif özelliğine uygun şekilde seçilmiş malzemeler olmasına dikkat edilmelidir. Paslanmaz çelikler ve özel bimetalik kaplamalar korozyona karşı alınabilecek en önemli önlemlerdir.
Kovan ve Vidalarda Aşınma
Kovan ve vidalarda aşınma kovan ile vidanın temas ettiği yüzeylerde meydana gelir. Aşınmada adhezyon ve abrazyon sebebiyle kovan ve vida arasındaki boşluk artar ve bu boşluk olması gereken değerlerin üzerine çıktığında proses şartları ve verim olumsuz yönde etkilenir. Plastik hammadde ile beraber kullanılan cam elyaf, kalsit gibi dolgu ve katkı maddeleri kovan ve vidanın aşınmasını hızlandırırlar.
Kovan ve vida birlikte çalışırken kovan içerisine beslenen hammadde, vidanın hatveleri arasında ve hatve üstlerinde sürtünmenin etkisi ile tutunarak ilerler. Hammadde içerisinde sürtünmenin etkisi ile tutunarak basınç bölgelerinde hem kovan cidarını hem de vida cidarını aşındırırlar. Bu aşınma ile kovan ve vida arasındaki boşluk giderek artar ve standart değerlerin üzerine çıkar. Kovan ve vida arasındaki boşluğun artması, basınç ile ileri sürülen, pompalanan hammaddenin kovan cidarı ile vida hatveleri arasından geri kaçarak proseste hem verim kaybına hem de aşınma hızının artmasına neden olur.
Kovan ile vida arasında olması gereken boşluk vida çapının yaklaşık binde beşi %0.5 kadardır. Eğer bu kovan ile vida arasındaki boşluk bu değerin üzerinde ise sistem çalışması gereken verimin daha altında bir verimle çalışıyor demektir.
‘’Unutulmamalıdır ki her zaman kovan ve vidada basıncın maksimuma ulaştığı noktalarda ve erimemiş plastiğin zorlanarak kovan ve vida içerisine alındığı besleme bölgesi civarındaki aşınmalar maksimumda gerçekleşir’’
ENJEKSİYON KOVAN VE VİDALARDA AŞINMA
Bu aşınma daha çok roket grubunun çalıştığı bölgede ve cam elyaf gibi soğuk aşındırıcılığı yüksek malzemelerin kullanıldığı şartlarda hammaddenin eriyene kadar kat ettiği mesafede gerçekleşir.
Enjeksiyonda kovan ve vida grubunun aşınması sebebiyle şu sorunlar ortaya çıkar;
* Mal alma süreleri uzar
* Eksik baskı, kalıbı dolduramama sorunları yaşanır
* Eriyik kalitesi ve homojenliği değişkenlik gösterir
* Basınç stabilitesi bozulur
* Sıcaklık kontrolü zorlaşır
* Kovan ve vida yüzeyinde pürüzlülüğün artması sebebiyle hammaddenin tutunması artar ve yanmalar bozulmalar başlar.
* Makinenin genel verimi düşer.
KOVAN VE VİDANIN AŞINMASINA ETKİ EDEN FAKTÖRLER
MEKANİK FAKTÖRLER
* Kovan ve vidada eğrilik olması
* Kovan, vida, redüktör ve kalıbın tam terazide olmaması
* Kovan ve Vida parçalı ise birleşme yerinde salgı olması
* Yanlış kovan veya vida geometrisi
* Yanlış tolerans ile işlenmiş parçalar
* Kovan ve vidanın yataklandığı bölgelerdeki bozukluklar
* Konstrüksiyona bağlı diğer hatalar
PROSESE BAĞLI FAKTÖRLER
* Kovanın her bölgede aynı düzeyde ısıtılamaması
* Prosese uygun olmayan ısıtma
* Çok yüksek kalıp ve filtre tazyiği ile çalışma
* Proses esnasında kovan ve vida içerisine kaçan toz, kum, metal tanecikleri vs.
* Proses şartlarına uygun olmayan kovan ve vida ile çalışma
Kovan ve vida içerisinde malzeme olmadığı halde uzun süre çalıştırılması
KOVAN VE VİDA AŞINMASINDA HAMMADDEYE BAĞLI FAKTÖRLER
* Hammadde karakteristiği (sert ya da yumuşak yapılı malzemelerin aşındırma oranları farklıdır)
* Hammaddenin yağlama kabiliyeti
* Katkı maddelerinin mevcudiyeti ve yapıları
* Dolgu maddelerinin cinsi, aşındırıcılığı
* Gerekli ön işlem yapılmamış olması
ENJEKSİYON SİSTEMLERİNDE KOVAN VE VİDANIN AŞINMA DURUMUNUN KONTROLÜ
KOVAN AŞINMA KONTROLÜ
Enjeksiyon sistemlerinde kovanın iç çapı delik komparatörü yardımı ile eğer mümkünse ise boydan boya değil ise özellikle roket grubunun çalıştığı bölgede ve besleme tarafından olmak üzere iki bölgeden ölçülerek kontrol edilmelidir. Ayrıca kovan içerisinde bulunan ve komparatörün ölçüm sınırları dışındaki çizikler ve yaralanmalar görsel olarak tespit edilerek raporlanmalıdır.
Kovanda şu kontroller yapılmalıdır;
* Kovanın herhangi bir yerinde çatlak yada kırık olup olmadığı kontrol edilmeli
* Flanş, meme bağlantılarının, faturalarının temas yüzeylerinde salgı olmamasına dikkat edilmelidir.
* Enjeksiyon memelerinin bağlantı dişlerinde herhangi bir bozukluk olup olmadığı kontrol edilmeli
* Enjeksiyon memesinde tıkanıklık olup olmadığı kontrol edilmeli
* Bağlantı cıvata dişlerinde deformasyon olup olmadığı kontrol edilmeli
* Soğutma sisteminin tıkalı olup olmadığı kontrol edilmeli
* Kovan doğrusallığı kontrol edilmelidir.
VİDA AŞINMA KONTROLÜ
Vidalarda aşınma, kovan ile hatve üstlerinde ve eğer korozif ya da aşındırıcılığı yüksek bir hammadde kullanılıyorsa hatve diplerinde meydana gelebilir. Vida aşınma durumunun ölçümü için kaç kaç bölgeden ölçü alınacağına vidanın dizaynı ve boyu etki eder. Standart vidalarda besleme, sıkıştırma ve dozajlama bölgelerinin her birinde en az iki noktadan ölçüm alınması gerekmektedir. Ayrıca roket grubunun bileziğinin aşınma miktarı mutlaka kontrol edilmelidir.
KOVAN VE VİDANIN TEMİZLENMESİ
Plastik işleme makinelerinin en hassas işlenen parçalarındandır. Çoğu zaman kovan ve vida arasında boşluk vida çapına göre 0.7mm ile 0.40mm arasında değişir. Dolayısı ile kovan ve vidanın ilk günkü hassasiyet ve verimlilikle çalışabilmesi açısından temizliği ve bakımı son derece önemlidir.
Kovan ve vida, hammadde değişimlerinde, periyodik bakım kontrollerinde önce yada uzun süreli duruşlarda mutlaka temizlenmeli ve uygun koruyucu yağlarla kaplanarak muhafaza edilmelidir.
Kovan yada vida mekanik olarak yada kimyasal yol ile temizlenmektedir. Kimyasal temizlikte kovan sistemden sökülmeden ve birbirinden ayrılmadan, normal proses şartlarında çalışan sistemdeki kovan ve vida içerisine beslenen bir temizleyici madde yardımı ile temizlik yapılır.
Mekanik temizlik ise; kovan ve vida makine üzerindeyken, içerisine farklı bir hammadde beslemek suretiyle, uygun bir katı temizleme kampaundu ile ya da makine üzerinden sökülerek ve birbirinden ayrılarak uygulanır.
Kovan ve vida üzerinde kısa ya da uzun süreli duruşlarda mümkün olduğunca hammadde bırakılmamalıdır.
Mekanik temizlemede dikkat edilmesi gereken hususlar:
Kovan ve vidalar makine üzerinden sökülürken kovan ve vida içerisinde mümkün olduğunca hammadde bırakılmadan sökülmelidir.
Sökme işleminden hemen sonra mümkünse kovan ve vida sıcak iken birbirinden ayrılmalıdır.
Birbirinden ayrılan kovan ve vida kesinlikle metal ya da sert zemin üzerine konulmamalıdır.
Kovan ya da vidalarda basit yöntemlerle temizlenemeyecek pislikler ve paslar profesyonel olarak polisajla temizlenmelidir.
Vidada çapaklar var ise sadece çapak olan bölge dikkatlice zımpara ile yumuşatılmalı ve mümkün olduğunda parlatılmalıdır.
Unutulmamalıdır ki kovan vida mümkün olduğunca parlak olmalı ve plastiğin takılabileceği hiçbir çapakçatlak ve bozuk yüzey bulunmamalıdır.